
Intake Design
OVERVIEW
Deputy Team Leader
2014-2015
Team Leader
2015-2016
GT-Suite
Star CCM+
Solidworks
Formula Student Intake Design
Low speed torque
Driveability
Manufacturing
Packaging
WORK
Overview
For my postgraduate thesis project I undertook the design and development of the intake system for the 2017 car.
​
This project not only needed to consider engine performance but also needed to consider overall vehicle packaging.
​
The design was developed using 1D engine simulation software and 3D CFD software, with the aim of improving torque performance.
During the project i worked closely with the exhaust designer to ensure the systems complimented each other and worked together.
​
Focus
The main focus was improving torque performance at low engine speeds, given the nature of the event low speed torque would allow the vehicle to accelerate out of low speed corners.
While overall torque performance was important, the engine's drive-ability was equally. Creating a wide flat torque curve to give a wide window of performance.
​
As previously mentioned packaging was a consideration, along with overall system weight, replacing 'stock' components with lighter alternatives.
​
Method
With dynamometer testing carried out, the first stage was to created a reliable and accurate 1D engine simulation model. Simulation results were able to correlate with real world testing.
​
Initial design was a result of extensive research into general intake design and Formula Student intake design. Using guidelines for design and having an understanding of airflow a great basis for design was formed.
A 1D/3D simulation was also built, coupling GT-Power and Star-CCM+ to help develop geometry and predict accurate performance.
Changes to the intake valve timing to reduce flow reversion through the intake valve completed the modifications.
RESULTS
23%
Peak torque Increase
16%avg
Torque increase
5000 rpm - 8000 rpm
2.5kg
Weight reduction
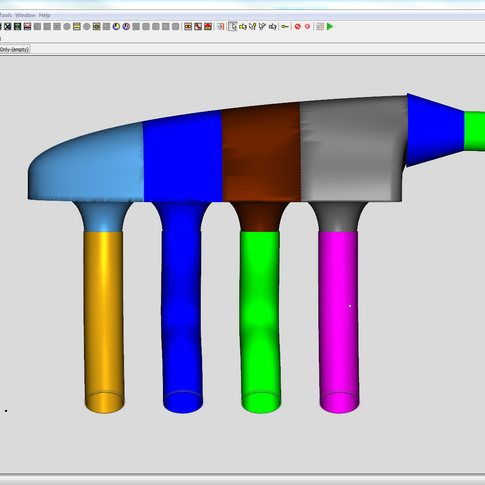
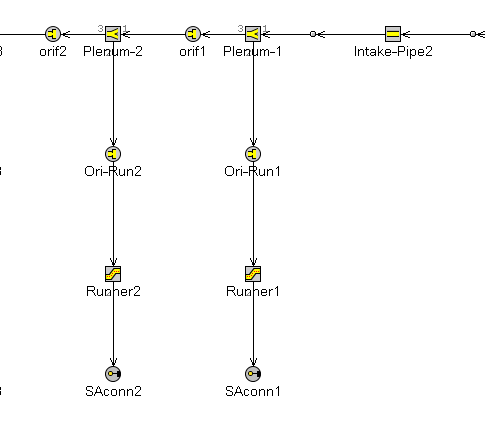


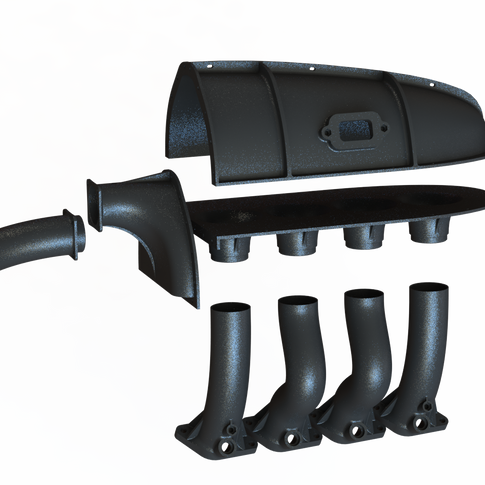



